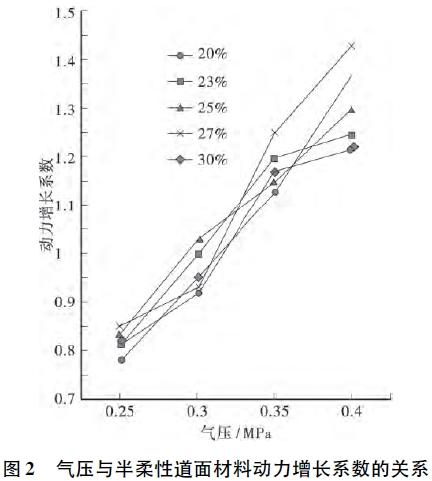
文章来源:微信公众号"沥青路面”
前言
灌注式半柔性道面材料是一种刚度大于沥青混凝土,小于水泥混凝土的复合道面材料,在兼具了两种材料优势的同时避开了它们的缺陷。半柔性道面不存在裂缝,而且受温度影响远远小于沥青道面,道面性能优异,因而在国内高等级公路上得到了广泛应用。对半柔性道面路用性能方面的研究较多,周启伟通过马歇尔稳定度试验和车辙试验对灌入式保水性沥青混凝土的抗车辙性能进行了研究。邓成等人发现,将超早强半柔性路面材料应用在市政道路交叉路口后,可以比较彻底地解决其车辙问题。阳晏等人主要研究了基体沥青混合料孔结构对半柔性路面材料路用性能的影响。王伟明等人通过试验评价了3种不同空隙率的半柔性路面材料的综合路用性能,结果发现其具有良好的高温稳定性、水稳定性和较强的抗疲劳能力。吴旷怀等人则对自主研发的冷拌半柔性材料进行了相关试验,同样发现其综合路用性能良好。但是将半柔性道面材料应用在飞机跑道上的示例和研究,还并不多见。徐贵等人运用ANSYS建立了半柔性道面结构模型,研究了半柔性道面在具有复杂起落架的大型飞机多轮荷载下的力学响应规律。丁润泽等人在对半柔性材料的力学特性及表层适用性进行试验的基础上,论述了采用半柔性材料进行机场沥青罩面的设计方法。周少乐等人进行了飞机荷载下半柔性道面的疲劳试验,运用有限元方法,提出了机场沥青道面加铺半柔性材料的结构设计方法。综合研读文献后发现,半柔性材料在机场道面上的运用具有一定的可行性,但针对半柔性道面抗冲击性能的研究,尚未查到相关资料。
本文在前人研究的基础上,运用SHPB等试验仪器,对空隙率为20%、23%、25%、27%和30%的灌注式半柔性道面材料的抗冲击性能进行了试验研究,为半柔性道面材料在飞机跑道上的进一步设计和运用提供了一定的理论依据。
试验概况
本文设计对空隙率为20%、23%、25%、27%和30%的半柔性道面材料进行静态抗压试验和SHPB试验。
静态抗压试验
制作大空隙母体沥青混合料圆柱形静态抗压试件(Ф100mm×100mm),取出试件并放置在压力机座上面,同时以2mm/min的速度垂直于试件加载,直到整个试件完全破坏,再读取荷载的最大值,精确到100N。试验时,每个试件必须放在中心位置,以免偏载影响试验结果。
SHPB试验
制作大小为300mm×300mm×40mm的方形试件,然后从中钻孔获取试件,以免试件模型太小难以控制空隙率。实验前,检查SHPB各试验系统是否正常,试打结束后,将测速计时仪清零,再对空隙率为20%、23%、25%、27%和30%共5种半柔性道面材料的试件分别进行气压为0.25、0.3、0.35,0.4MPa的动态力学性能测试,实验结束后用DHDAS软件将信号做滤波处理,消除干扰信号。
试验结果与数据分析
试验结果
通过运用DHDAS系统对试验数据进行滤波以及Matlab软件进行整理后得到了试验数据。因数据量巨大,只列出各试件3次试验的平均值。可以看出:在相同气压冲击下,不同空隙率的半柔性道面材料平均应变率相差较小。
空隙率对半柔性道面材料动态力学性能的影响
首先,通过对各个空隙率半柔性道面材料的峰值应力进行比较后发现,0.25MPa和0.3MPa两种气压条件下,峰值应力均有C>D>E>B>A,说明试验中空隙率为25%的半柔性道面材料动态抗压强度增强效果最为明显,其次分别是空隙率为27%、30%、23%、20%的半柔性道面材料。较空隙率20%的半柔性道面材料而言,空隙率为25%、27%、30%、23%的材料在气压为0.25MPa气压条件下的峰值应力分别提高了22.95%、20.87%、6.04%、1.79%;0.3MPa条件下,峰值应力分别提高34.92%、17.25%、14.41%、11.56%。而在0.35MPa和0.4MPa两种气压条件下时,各空隙率半柔性道面材料的峰值应力有D>C>E>B>A,空隙率为27%的半柔性道面材料动态抗压强度超过了空隙率为25%的材料。较空隙率为20%而言,空隙率为27%、25%、30%、23%的半柔性道面材料在气压为0.35Mpa条件下的峰值应力分别提高了23.41%、17.84%、6.43%、4.85%;0.4Mpa条件下,峰值应力分别提高了35.56%、28.18%、24.02%、4.98%。
从SHPB试验结果来看,空隙率为20%和23%的半柔性道面材料峰值应力一直是最小的两个,主要是由于母体沥青混合料空隙率较小,在进行灌注砂浆的时候并不能够达到完全灌注,导致材料内部有空隙(在进行钻孔取芯时已经发现内部存在空隙),降低了材料自身的粘结力和抗力,致使材料的抗冲击性能下降。虽然空隙率为30%时的半柔性道面材料空隙率足够大,水泥砂浆能够顺利灌入,但是由于空隙率影响材料的碎石级配,空隙率高,碎石掺和比例大,配制空隙率为30%的半柔性道面材料时碎石与细砂的掺和比已达到96%,其中5~10mm碎石达到了58%,这使得材料内部骨料之间不能很好的嵌挤,沥青与沥青之间不能很好的粘黏,致使材料自身摩阻力降低,虽然填充了足量水泥砂浆,但是对材料的抗冲击能力提高有限。但是相对于空隙率20%及23%的半柔性道面材料,空隙率30%时的骨料级配较大,因此抗冲击性能相对于两者都较好。空隙率为25%及27%的半柔性道面材料分别在较低应变速率(气压值为0.25MPa和0.3MPa)和较高应变速率(气压值为0.35MPa和0.4MPa)的作用下峰值应力最大。空隙率为25%和27%的材料,空隙率适中,水泥砂浆能够顺利灌注且不留下空隙,同时这两个空隙率条件下的碎石级配也适中,所以二者抗冲击性能相比于其他3个空隙率较好。空隙率25%的半柔性道面材料在较低应变速率作用时,由于材料内部碎石充分嵌挤,摩阻力和沥青的黏聚力抵抗冲击的作用大于水泥的凝聚力,因此峰值应力大于空隙率27%的半柔性道面材料。当较高应变速率作用时,水泥凝聚力起主导作用,因而此种条件下空隙率为27%的材料峰值应力大。
同一空隙率下,半柔性道面材料峰值应力随着气压值的变大而变大;随着气压值的增加,半柔性道面材料的动态抗压强度的增长速率减缓。这主要是由于材料本身的性质,在材料制作和养护的过程中材料内部会产生微裂缝和气孔,当较低应变速率作用在试件上时,材料内部的裂缝不断发展,裂缝连通的路径选择在当前应变率条件下最薄弱的环节上发展。随着气压的增大,作用在试件上的应变率也增大,当较高的应变速率作用在试件上时,裂缝的发展不再沿着原有发展路径进行,而是选择在此时较高应变率条件下试件的最薄弱环节上进行。当应变速率变大时,试件破坏时内部的细微裂缝不能及时在试件内部扩展,因而导致材料中的骨料破坏。应变速率越高,材料内部骨料破坏的越多,这也是材料峰值应力随应变速率增大而增大的原因。
空隙率与动力增长系数的关系
发现各个空隙率下的半柔性道面材料的动力增长系数都随着气压的增大而增加,动力增长系数最大达到了1.43。在同一气压之下,5个不同空隙率大小的半柔性道面材料动力增长系数相差不大,这说明此时半柔性道面材料的抗冲击性能和空隙率的变化并没有明显的关系。
破坏形式分析
半柔性道面材料试件在受到荷载冲击后,试件破坏形态主要有表面完好、边缘破裂、破碎和粉碎4种。从表面完好到粉碎的过程,体现了空隙率在半柔性道面材料中中明显的阻裂和粘结作用。
可以发现,空隙率为20%和23%的试件在4种气压冲击下破坏时更容易被压碎,而空隙率为27%的试件在0.25MPa气压下破坏形态表现为表面完好,在0.4MPa气压下也表现为破碎状态,而不是与其他四种空隙率一样表现为粉碎,由此反映出空隙率27%的半柔性道面材料具有较强的韧性,抵抗冲击的能力更强。
半柔性道面材料是由大空隙基体混合料与水泥砂浆组成的新型复合材料,其性质已不再是单一的沥青混合料和水泥砂浆的性质。在受到0.25MPa气压下的子弹冲击时,五组试件破坏形态最严重的的仅是边缘破裂,由此可见0.25MPa气压的冲击对试件的结构破坏并不严重,材料自身的抗力、粘结力、黏聚力和摩阻力足以抵抗较低荷载的冲击。随着气压增大,较高的应变速率作用在试件上,其自身抗力、粘结力、黏聚力和摩阻力不足以抵抗荷载的冲击,最终出现破碎形态,甚至出现骨料破坏的粉碎形态。
从各个试件的破坏形态来看,空隙率27%的试件总体表现较好,在0.25MPa气压冲击下的所有试块全部完好,在0.4MPa气压冲击下的试件仅有一块破坏形态接近粉碎,其余两块仅达到破碎形态。单从破坏形态来看,空隙率为27%的材料在抗冲击性能上要优于其他四个空隙率的材料。
结论
①通过对试验结果进行分析比较,各空隙率下的半柔性道面材料的峰值应力随着气压的增加而增大。较低气压冲击作用下(0.25MPa和0.3MPa),空隙率为25%的半柔性道面材料峰值应力最大,其后的空隙率依次为27%、30%、23%、20%。在较高气压冲击作用下(0.35MPa和0.4MPa),峰值应力最大的一组变为了空隙率为27%的一组,其后的空隙率依次为25%、30%、23%、20%。空隙率25%的半柔性道面材料在较低应变速率作用时,由于材料内部碎石充分嵌挤,摩阻力和沥青的黏聚力抵抗冲击的作用大于水泥的凝聚力,因此峰值应力大于空隙率27%的半柔性道面材料。当较高应变速率作用时,水泥凝聚力起主导作用,因而此时空隙率为27%的材料峰值应力更大。
②不同的应变率条件下,试件内部裂缝发展的路径并不相同,应变率较大时,试件内部的细微裂缝不能及时在试件内部扩展,导致了试件中的骨料破坏,且应变率越高,骨料破坏越多。这也是材料峰值应力随应变速率增大而增大的原因。
③半柔性道面材料动力增长系数随着气压的增大而不断变大,最大达到1.43(空隙率为27%的一组)。但相同气压下,半柔性道面材料的动力增长系数与空隙率没有明显的关系。
④从破坏形态来看,空隙率为27%的试块较其他4个空隙率的试件要好。综合来看,空隙率为27%的半柔性道面材料抗冲击性能优于其余4个空隙率的材料。