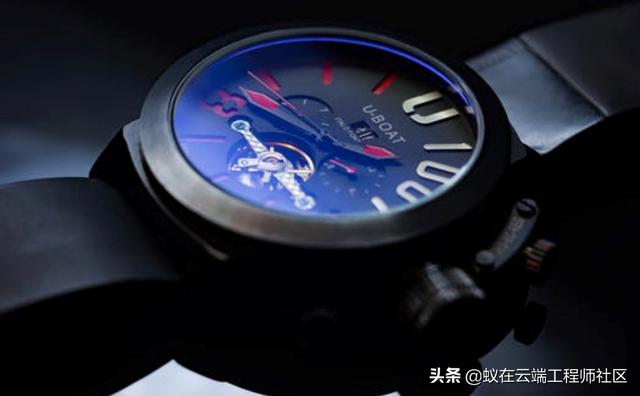
上一篇文章种蚂蚁先生跟大家详细分析了产品成本的组成,其主要分为材料成本和制造成本两个部分。 然而要得到制造成本,则必须有标准工时数据。那么标准工时究竟是什么呢?
标准工时制: 标准工时是在标准工作环境下,进行一道加工工序所需的人工时间。其具体可以分为TR准终工时、TE人工工时、TM机器工时。标准工时是生产费率计算的基础,没有标准工时就没有生产费率。
准终工时:生产产品切换时准备和结束工作所需要的时间。主要指:熟悉工艺文件、领取毛坯、安装夹具、调整机床、拆卸夹具等所消耗的时间。(单个零件的上下料时间不计算在内)
人工工时:加工单个零件时,所耗费的直接人工工时。主要只上下料、程序启动、实际操作等时间。(物料的批量搬运时间不算在内)
机器工时:加工单个零件时,所耗费的机器时间。(这里的机器时只工位的概念,并不是只具体的某一台机器)
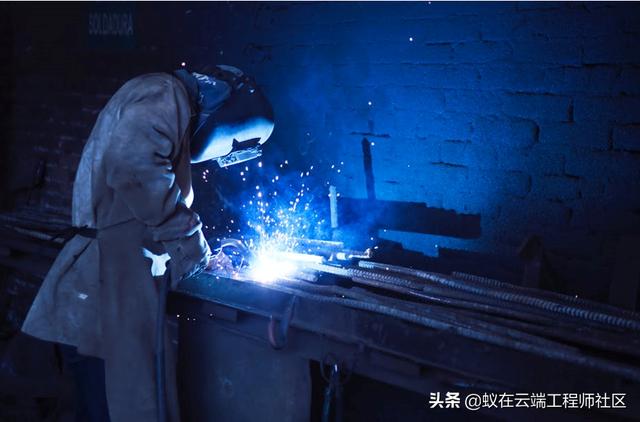
这些看上去是不是很简单呢?让我们一起来学习几个案例吧!
案例一 单工位手工操作 A产品:
生产时,需要1位操作者用2分钟准备号工具,使用5分钟的锤子,然后使用3分钟的扳手。
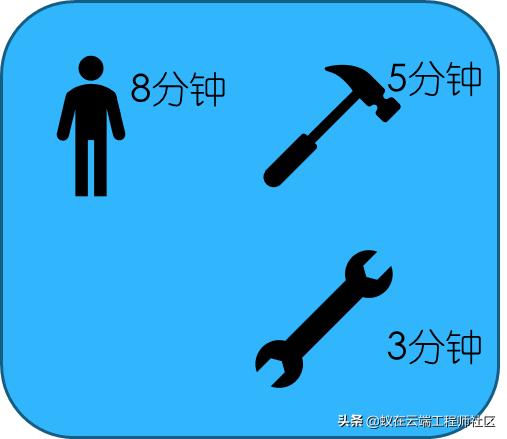
A产品工时
准终工时=2分钟
人工工时=5+3=8分钟
机器工时=人工工时=8分钟
这里要注意:我们在计算机器工时时必须把工位看成一个整体。虽然锤子只用了5分钟,扳手只用了3分钟。 但对于这个工位的占用时间时8分钟。
案例二 单工位 人工装夹 机器人焊机 B产品:
- 操作者用6分钟更换模具(机器人停机)
- 操作者用5分钟上料(机器人停机)
- 机器用20分钟焊接(操作者到其他工位操作其他产品)
- 操作者用3分钟进行下料(机器人停机)
- 操作者用5分钟拆卸模具
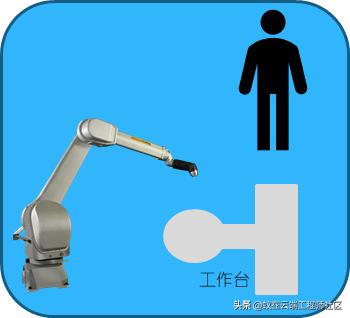
B产品工时
准终工时=6+5=11分钟
人工工时=5+3=8分钟
机器工时=5+20+3=28分钟
注意点:更换模具是一批次才更换一次的,因此通常不能算入单件工时,而应计算入准终。(在单件定制化生产的情况下,才会将换模时间计算到单件工时中。)
人工工时:操作者在这个工位,除了上下料的8分钟外,其余时间是做其他产品。因此,B产品的人工工时只能算8分钟
机器工时:很多人会误把机器工时设成20分钟。 机器人虽然只工作了20分钟,但另外8分钟是停机浪费掉了。因此,计算机器工时,应等于20+8
案例三 双工位 人工装夹 机器人焊接 C产品:
- 操作者在工位1用8分钟上下料(机器人在工位2焊接)
- 机器在工位2用10分钟焊接(操作者做完工位1后等待)
- 操作者在工位2用8分钟进行上下料料(机器人在工位1焊接)
- 机器在工位1用10分钟焊接(操作者做完工位2后等待)
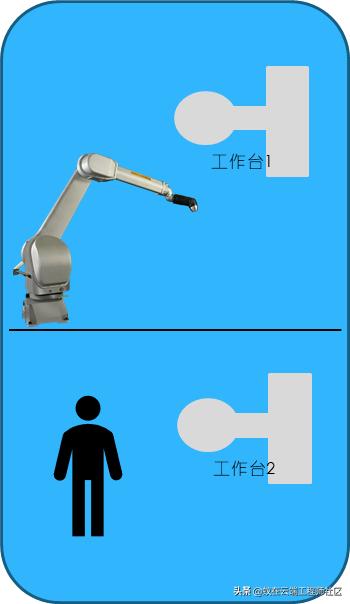
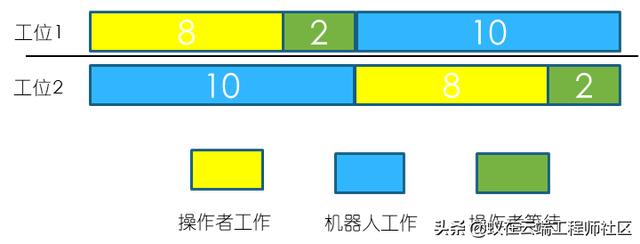
C产品工时
人工工时=10分钟
机器工时=10分钟
注意点:很多人容易将工时算成20分钟。而实际上20分钟里,这个人+机器共产出了2个零件。
此外,也有很多人会将人工工时=8,机器工时=10。 要注意的是,人员闲置也是一种浪费成本,必须计算在内。
案例四 双工位 人工装夹 机器人焊接 D/E产品:
- 操作者在工位1用8分钟上下料(机器人在工位2焊接)
- 机器在工位2用10分钟焊接(操作者做完工位1后等待)
- 操作者在工位2用9分钟进行上下料料(机器人在工位1焊接)
- 机器在工位1用12分钟焊接(操作者做完工位2后等待)
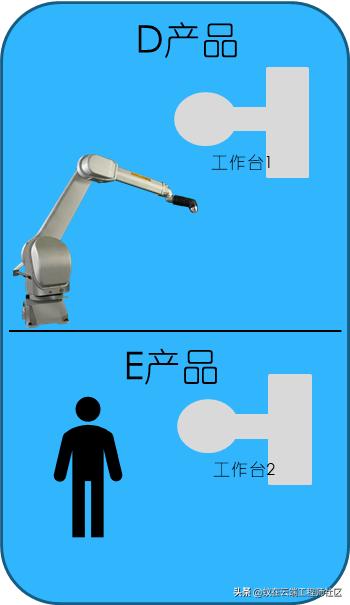
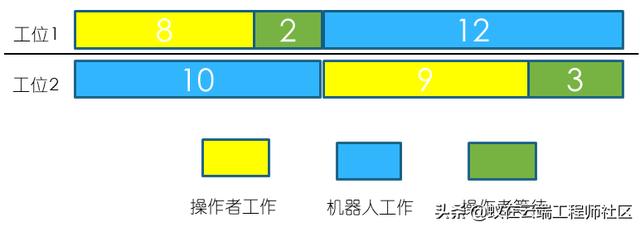
D产品工时
人工工时=12分钟
机器工时=12分钟
E产品工时
人工工时=10分钟
机器工时=10分钟
注意点:与上面的案例相同,闲置时间必须被计算在内。 但人员的闲置时间是要如何分摊呢?也有人会将D产品的人工工时=10,机器工时=12,E产品人工工时=12,机器工时=10.但按照蚁在云端的操作习惯,因为实际机器工时>人工工时,因此我们通常会将人工工时=机器工时。 这样做的最大好处就是便于计算。
看完这些,您是否对工时的定义和分配有更清楚的了解了呢?如果您有任何的疑问,欢迎来到蚁在云端工程师社区与我们交流。
作者:蚂蚁先生
原创:蚁在云端