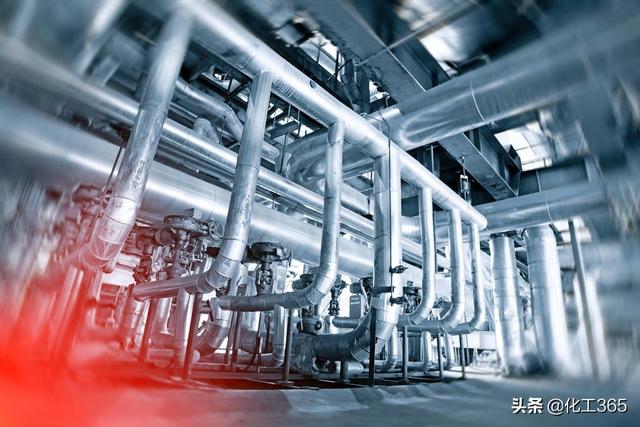
HAZOP 与检查表的区别
HAZOP 分析可以在工厂运行周期内的任何时间段进行,既适用于设计阶段,也适用于在役的工艺装置。
在化工项目的设计阶段采用HAZOP 方法进行分析,能识别设计、设备及操作程序中的潜在危险,比如装置设备是否装有安全联锁 , 在操作规程中是否明确规定保持正压操作等,将风险尽可能地消灭在设计阶段,节省投资 ;对石油化工企业的在役生产装置应用 HAZOP 分析,可深入分析化工装置的设计、开车、运行、停车和检维修等各个阶段的安全隐患及可操作性问题,使安全管理人员和操作人员对工艺过程及生产设备有系统、深入地了解,清楚存在的风险及应采取的措施,为装置的日常生产与维护以及风险管理提供指导。
日常生产中,很多人习惯凭经验、检查表进行隐患排查,不理解HAZOP 的好处。利用安全检查表法对装置进行过程安全检查是一项依赖专家对风险和有关问题的了解进行核查的方法,检查表中所检查的项目是已知的问题,不能检查出未知的隐患。另外,检查表法不是一项结构化的系统检查,其使用的时间远比 HAZOP 小组分析所用的时间要短得多。
通常,安全检查表用来普查隐患的“原因”和“后果”,而 HAZOP用来揭示系统性的风险,即找到检查表中的“原因”与“后果”的内在联系以及防止这些风险发生的措施。
HAZOP 的应用效果
HAZOP 分析方法在世界范围内已经得到广泛的应用,许多国际大型石化企业要求所有新装置都要在设计阶段进行 HAZOP 研究 ;所有改、扩建装置都要进行 HAZOP研究 ;流程规模越大、越复杂,越需要 HAZOP 研究 ;在役装置如果没有任何变更,每隔 5 年也要进行HAZOP研究。许多国际化工程公司将 HAZOP 视为确保设计和运行完整性的标准设计惯例,甚至很多国家要求将化学工业的 HAZOP 分析作为防止重大化学事故计划的一个重要部分。
目 前,HAZOP 分析在我国还属于起步阶段,但一些有实力的企业已经开始尝试使用 HAZOP 分析。笔者曾经参与对中石油锦州石化公司的气分车间的 HAZOP 分析,该车间装置包括一套气分、二套气分、西山罐区和液化气站,共计分析管道及仪表 (P&ID) 流程图 23 张,划分工艺节点 49 个,提出建议措施36 项共计 80 余条,其中风险等级为高度的有 2 项,风险等级为中度的有 26 项。企业全部采纳并列入整改计划,通过对在役多年的装置实施 HAZOP 分析,企业重新认识自身的装置,对发现的重大隐患及时制定并采取了措施,从而保证装置的安全平稳运行。
本文由化工365二次编辑整理