
齿条:螺纹连接的设计和计算是否正确?
如果我们真的想要节约装配成本和时间的话,那么我们首先就需要去选择设计正确的齿条螺钉。那么这时候就紧接着产生了第二个问题:我们应该如何评估并优化这种设计。
当我们去观察比较齿轮和齿条这两种典型的机床零部件的时候,他们看上去长得完全不一样。齿轮是圆形的,中心对称的,而齿条却是长条状的。然而,当我们去考察其基本的工作原理的时候,我们就会发现,齿条实际上就是一个直径无限大的齿轮。正是因为这种特殊性,从而使得齿条和齿轮的分级和设计准则完全一致,甚至还包括了对它们的公差要求和强度要求。
但是,如果我们现在反过头来考察他们的生产制造工艺时,我们却又会发现,齿条的热处理和齿轮热处理工艺大相径庭。这其中的原因在于,对于齿条而言,它的工作面这一端是无数的齿,而它另一端的安装面区域却是整块的材料,因此,在进行热处理加工的时候,齿条的工艺复杂程度要远远高于齿轮。
基于上面提及的共同点和不同点,我们才能理解,为什么VDI2230技术标准里面,哪怕螺钉都是位于同一公差带,甚至装配内径都是一致,而齿条的螺纹连接的技术要求,却依然不同于齿轮的螺纹连接,要复杂很多。 譬如在VDI准则里面写着,当固定齿条的一排螺钉与应力流方向平行的时候,实际分布到每个螺钉上的应力却并不是均匀分配的。这排螺钉的最外两端的两颗螺钉,需要承载的荷载是最大的。
实践是原理的试金石。
在过去的若干年里,ATLANTA作为传动领域的领军企业,为了通过以理论联系实际的方式来解决难题,曾经进行了成千上万次的研究实验。在此期间,我们利用计算机辅助的建模程序,模拟了数不清的应用场景,包括螺钉的数量,大小,带辅助定位销,不带辅助定位销,甚至包括接触面,承载面的不同形状,以及齿条的制作工艺。这里面就只有一个唯一的例外,那就是以上提及的实验和计算,均不涉及到正齿和斜齿的模拟,否则的话,情况将会过于复杂。
在这个模拟程序中,我们主要计算的是螺钉所能产生的“位移阻力(Movement Resistant Force)”,针对这个专用名词,亚特兰传动技术有限公司的研发部经理,Mr.Marcus Timmermann做出了如下的解释:在通常的应用条件下,如果让一根装配好的齿条产生位移,在这个瞬间所对应的最大推力,就是上文所说的“位移阻力(MRF)”。由此,我们就可以将螺纹连接的安全设计定义为,齿条螺纹需要设计得足够强大,从而在设备急停的时候,对齿条上的定位销不产生任何影响。
“如果我们可以大幅度的减少装配工序,以及与此相关的物流消耗,那么我们就可以非常显著地减少装配总用时。因此,螺纹连接的设计就显得非常地重要,因为它需要负责引导由床身传向齿条的应力流”Mr.Timmermann进一步解释到。在此,应用工程师就需要注意,在螺纹连接中,不应产生任何额外的多余应力。在拉伸的时候,不允许有额外的横切力作用在螺纹上;或者在拉伸过程中不会侧向拉歪。螺钉一旦拉歪,那么就会产生内应力以及额外的荷载力,从而导致齿轮在齿条上的脱轨,或者造成螺钉的松动。
所需螺钉越少,可装配距离越长
“如果想让齿条产生的微量位移在完全可控的范围之内,那么此时装配工的认知水平就起了绝对重要的作用。可是,按照一般人的思维,大部分的装配工都会想当然地认为,螺钉的尺寸大小,在机床的装配过程当中,不会产生啥大的区别和影响。”Mr. Timmermann苦笑道。
举个例子:
按照我们的工业标准,1根1米长的模5的齿条,一般需要钻8个M12的装配孔。如果此时可以产生的位移阻力为100%的话,如果我们采用了16个M12的螺钉,共计可以达到200%的阻力。但是此时我们却需要2倍的长度,以及2倍的装配用时,才可以完成设计目标。
而如果我们继续保持2倍的长度,而此时我们采用2米的同模级齿条,那么我们仅仅需要8个M16的螺钉,在我们满足达到200%的位移阻力的同时,装配的时间也与1根1米的齿条相同。
这一点其实比较好理解,当我们装配长距离的齿条时,如果我们不去使用1米的齿条,而是采用2米的齿条去装配的话,并不意味着所需要的螺钉和接缝会自动多一倍,也不意味着所需要的装配时间也会多一倍。
除此以外,对于有经验的装配工来说,2米长的齿条的长度误差只是1米的齿条的1.3倍,这也就意味着,如果拿2米的齿条来装配长距离设备的话,其装配的总精度要远远优于1米齿条装配的设备。
箴言:
齿条的可控位移取决于设计人员,而不是取决于齿条本身
在齿条上力量的传递不仅仅是发生在齿面接触上,而且还发生在螺纹连接上。因此,位移阻力成为了决定因素之一
不管是大螺钉,还是小螺钉,只要它们数量相同,那么所需的装配时间也相同长距离的齿条会使用更多的螺钉,可以承载更大的位移阻力,因此我们要避免采用短齿条。如果设计正确,实际上安装定位销这道工序完全可以被省略。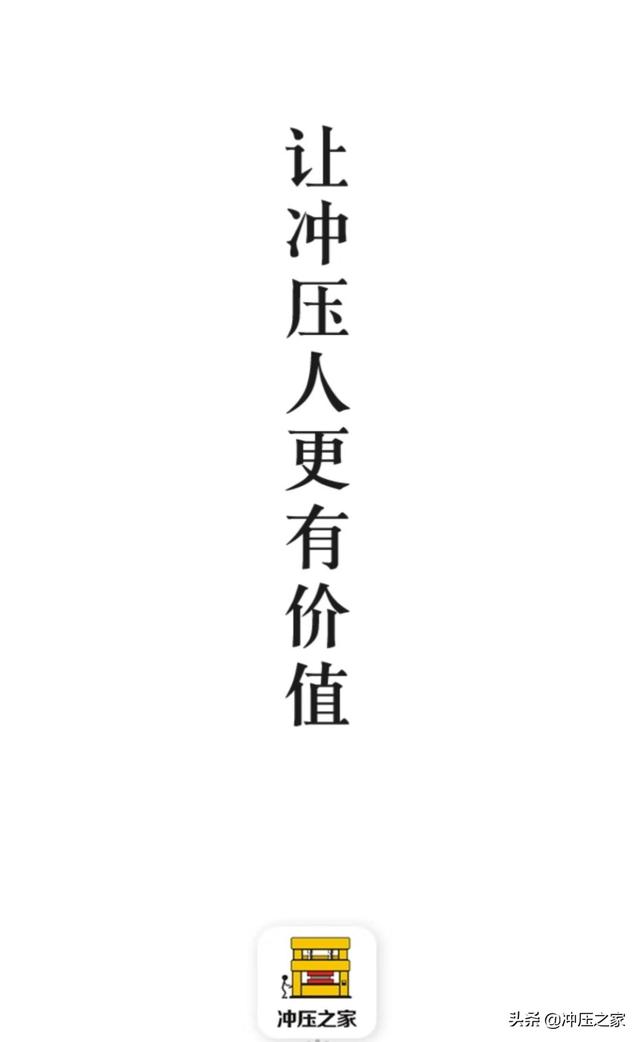