在金属3D打印过程中,可能会出现大量设备操作者试图避免的问题,包括孔隙、残余应力、致密度、翘曲、裂纹及表面光洁度等。下面我们来谈谈这几种常出现的问题。
1、表面光洁度
在金属3D打印件被使用或放置在展柜之前,它已经经历了大量类似CNC加工、喷丸或喷砂等后处理工艺,因为3D打印出来的金属件表面是凹凸不平的。
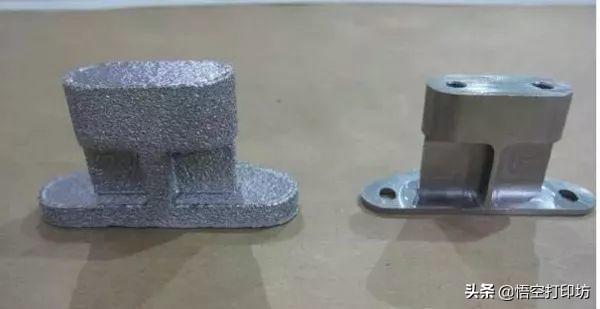
图3 EBM工艺3D打印Ti-6Al-4V钛合金支架机加工前后
受工艺本性的影响,直接能量沉积法生产的是接近最终形状的零件,它必须进行CNC处理以满足相应规格要求。粉末床熔融方式生产的零件更接近其最终形状,但是其表面依然粗糙。为提高表面光洁度,可采用更细的粉末、更小的层厚。
2、孔隙
由于金属3D打印工艺本身或者粉末原因,可能会引起在零件3D打印过程中,内部会形成非常小的孔穴孔隙。这些微孔会降低零件的整体密度,导致裂纹和疲劳问题的出现。
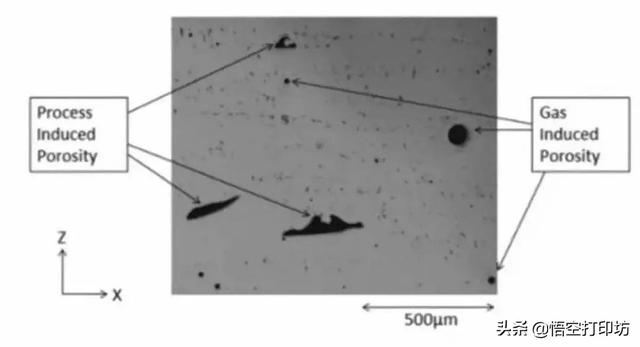
图4:光学显微镜下产品内部孔隙
上图光学显微镜结果比较了工艺引起的熔融不完全孔隙和粉末原料带来的孔隙。
在雾化制粉过程中,气泡可能在粉末的内部形成,它将转移到最终的零件中。所以,从优秀供应商手中采购金属粉末材料相当重要,优质粉末将减小零件形成孔隙的几率。
更常见的是,3D打印过程本身会产生小孔。比如当激光功率过低,会导致金属粉末没有充分熔融。当功率过高,会出现金属飞溅的现象,融化的金属飞出熔池进入到周围区域。
3、密度
零件的致密度与孔隙量成反比。零件气孔越多,密度越低,在受力环境下越容易出现疲劳或者裂纹。对于关键性应用,零件的致密度需要达到99%以上。
除了前文提到的控制孔隙量的方式,粉末的粒径分布也可能影响到零件致密度。球形颗粒不仅会提高粉末的流动性,也可以提高零件致密度。此外,较宽的粉末粒径分布允许细粉末填充于粗粉末的间隙,导致更高致密度。但是,宽粉末粒径分布会降低粉末的流动性。
4、残余应力
在金属3D打印中,残余应力由冷热变化、膨胀收缩过程引起。当残余应力超过材料或者基板的拉伸强度,将有缺陷产生,如零件有裂纹或者基板翘曲。
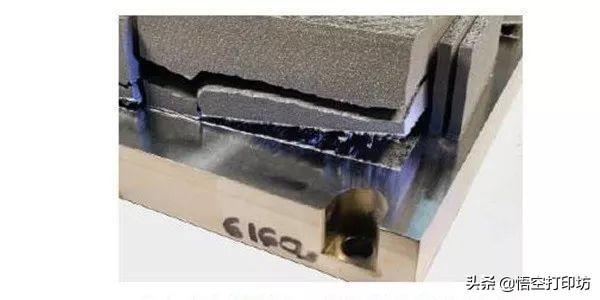
图5:残余应力导致3D打印钛合金件从平台脱离
残余应力在零件和基板的连接处最为集中,零件中心位置有较大压应力,边缘处有较大拉应力。
可以通过添加支撑结构来降低残余应力,因为它们比单独的基板温度更高。一旦零件从基板上取下来,残余应力会被释放,但这个过程中零件可能会变形。
劳伦斯利福摩尔国家实验室科研人员提出了一种降低残余应力的方法,为了控制温度起伏,可采取减小扫描矢量长度的方式代替连续激光扫描。根据零件最大截面旋转扫描矢量的方位也许能起作用。
6、裂纹
除了零件内部孔隙会产生裂纹外,熔融金属凝固或某片区域进一步加热也会出现裂纹。如果热源功率太大,冷却过程中可能会产生应力。
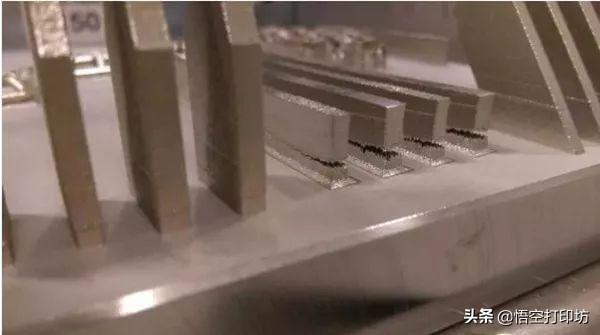
图6 粉末床熔融工艺中应力导致断裂
分层现象有可能会出现,导致层间发生断裂。这可能是粉末熔化不充分或熔池下面若干层重熔引起的。有些裂纹可以通过后期处理来修复,但分层无法通过后处理解决。相应地,可采取加热基板的方式来减少这个问题的出现。
7、翘曲
为了确保打印任务能顺利开始,打印的第一层熔融在基板上。当打印完成后,通过CNC加工使零件从基板上分离。然而,如果基板热应力超过了其强度,基板会发生翘曲,最终会导致零件发生翘曲,会有致使刮刀撞到零件的风险。
其他问题
其他变形,比如膨胀或者球化,也可能出现在金属3D打印过程中。膨胀发生于熔化的金属超出了粉末的高度。类似地,球化为金属凝固成球形而不是平层。这和熔池的表面张力有关,它可以通过控制熔池的长度-直径比小于1-2来减弱。
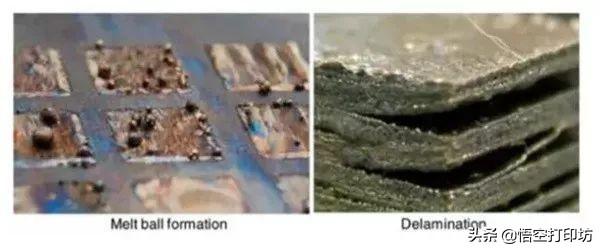
图8:3D打印不锈钢球化与分层
在金属3D打印时避免各种问题仍需要大量的工艺知识积累和不断尝试。每个零件都需要修改设备参数,通常导致设备操作者需多次打印同一个零件,直至克服翘曲、裂纹、孔隙等问题。一旦打印完成,需要对零部件进行测试,确保其满足相关标准。
以上就是悟空打印坊为大家介绍的有关3D打印金属材料模型过程中常见问题的分析,希望大家喜欢。
悟空打印坊,一站式 ,提供200多种材料的0.05mm精度的3D打印手板模具,3D打印动漫手办,3D打印建筑模型,3D打印人像,3D打印沙盘模型等打印服务。