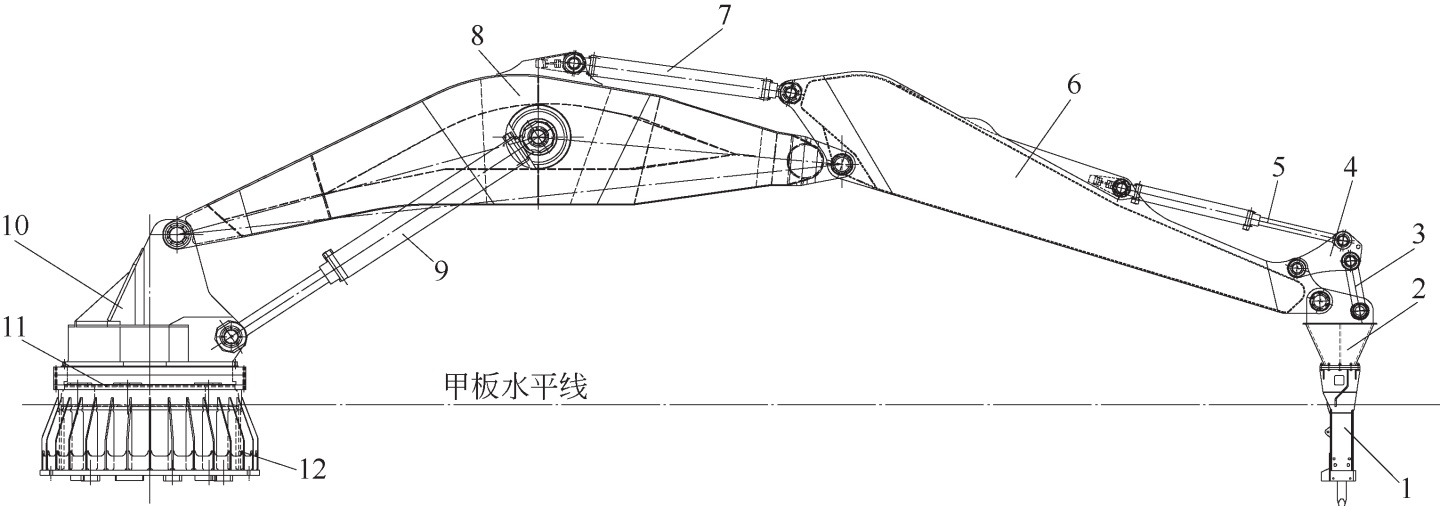
刘 斌 徐沪萍 王 磊
武汉理工大学物流工程学院 武汉 430063
摘 要:以配备液压破碎锤的反铲挖泥船反铲挖泥机为研究对象,简单介绍加装液压破碎锤方案,然后运用动力学理论和相关的动态仿真软件,通过建立反铲挖泥机的刚柔耦合模型,模拟计算获得反铲挖泥机作业过程中臂架结构的主要节点应力分布情况以及危险节点的动态响应应力历程,为反铲挖泥机加装破碎锤提供一定的参考。
关键词:反铲挖泥机;动力学;刚柔耦合;动态应力
中图分类号:TH213.4 文献标识码:A 文章编号:1001-0785(2018)07-0108-05
随着我国疏浚行业的逐步发展,与之配套的疏浚装备面临的考验也越来越多,目前在大型反铲挖泥机头部配备液压破碎锤进行水下破碎作业,能有效缩短施工周期,值得研究、推广。本文针对HB10000 型液压破碎锤结构体与挖泥机臂架系统本身连接的可行性进行了分析和研究,运用动力学理论以及相关的仿真软件(ADAMS)进行臂架结构的动力学分析。
1 反铲挖泥机加装破碎锤结构方案
配备有液压破碎锤(HB10000 型)挖泥船挖泥机装配总图如图1 所示。新设计的破碎锤支承架结构为箱型结构,其与小臂头部和直连杆连接的销孔位置镶有耐磨衬套,连接销轴和端盖均采用原铲斗与小臂及直连杆连接的销轴。当需要破碎锤进行水下破岩作业时,拆卸铲斗连接销轴,安装破碎锤支承架,然后再安装破碎锤。
2 反铲挖泥机刚柔耦合虚拟样机
对于诸如大臂、小臂、连杆、破碎锤支承架需要重点研究关注其结构强度的构件,把它们作为柔体处理;液压缸的闭锁功能使液压缸皆处于固定状态,一般只需要在模型仿真分析中提取得到其作用力,因此,将液压缸组作为刚体处理;同时将破碎锤作为刚体处理。利用Ansys 建立有限元模型生成相应的MNF 模态中性文件,将对应的构件通过ADAMS接口读取后,添加约束关系。添加约束后的BA1100 反铲挖泥机刚柔耦合虚拟样机臂架系统虚拟模型[1,2] 如图2 所示。
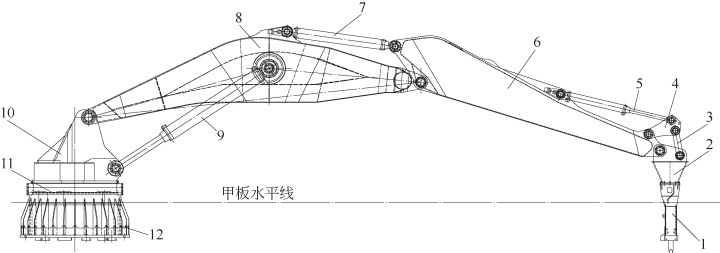
1. 破碎锤 2. 破碎锤支承架 3. 直连杆 4. 铲斗连杆 5. 铲斗液压缸(2 个) 6. 小臂
7. 小臂液压缸(2 个) 8. 大臂 9. 大臂液压缸(2 个) 10. 转台 11. 回转支承 12. 支承圆筒
图1 加装破碎锤挖泥机装配总图
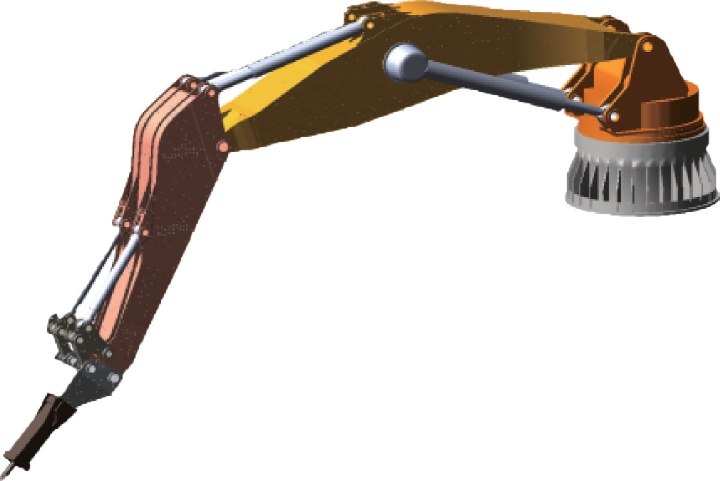
图2 反铲机臂架刚柔耦合虚拟样机
3 工况确定及载荷计算
3.1 工况分类
选择5 种典型工况进行分析:工况1 反铲机处于10 m 幅度、水下5 m 挖深位置进行凿岩作业,水位线以上的臂架结构受到蒲氏8 级风力作用,水位线以下的臂架结构受到水流作用(流速为3.3 m/s),考虑船舶横倾1°;
工况2 反铲机处于10 m 幅度、水下25 m 挖深位置进行凿岩作业,水位线以上的臂架结构受到蒲氏8 级风力作用,水位线以下的臂架结构受到水流作用(流速为3.3 m/s),考虑船舶横倾1°;
工况3 反铲机处于20 m 幅度、水下25 m 挖深位置进行凿岩作业,水位线以上的臂架结构受到蒲氏8 级风力作用,水位线以下的臂架结构受到水流作用(流速为3.3 m/s),考虑船舶横倾1°;
工况4 反铲机处于25 m 幅度、水下5 m 挖深位置进行凿岩作业,水位线以上的臂架结构受到蒲氏8 级风力作用,水位线以下的臂架结构受到水流作用(流速为3.3 m/s),考虑船舶横倾1°;工况5 反铲机处于25 m 幅度、水下20 m 挖深位置进行凿岩作业,水位线以上的臂架结构受到蒲氏8 级风力作用,水位线以下的臂架结构受到水流作用(流速为3.3 m/s),考虑船舶横倾1°。
3.2 载荷计算
3.2.1 自重载荷
反铲机臂架系统结构的自重载荷

式中:G1 为转台自重,G2 为液压缸组自重,G3 为大臂结构自重,G4 为小臂结构自重,G5 为液压破碎锤结构自重,G6 为铲斗连杆结构自重,G7 为直连杆结构自重,G8 为液压破碎锤支承架结构自重。
3.2.2 外部载荷
反铲机进行凿岩作业时,外部载荷主要有锤体结构的反作用力、臂架系统结构受到水的浮力以及水流的冲击、海风对臂架系统的风阻力、风浪引起的船舶倾斜载荷。
1)破碎锤反作用力
阿特拉斯科普克液压破碎锤HB10000 参数为机身质量10 000 kg、驱动液压16 ~ 18 MPa、打击频率250 ~ 380 次/min、最大输入功率159 kW、缓冲力170 kN。取HB10000 破碎锤最小反作业力为170 kN。
2)水的浮力
挖泥机在水中进行破岩作业时,臂架系统还受到水的浮力作用,有

式中:ρ 为水的密度,V 1 为液压破碎锤体积,V 2为破碎锤支承架的体积,V 3 为小臂液压缸体积,V 4 为小臂于水中部分的体积,g 为重力加速度。
3)迎风阻力和水流冲击载荷
迎风阻力和水流冲击载荷大小与反铲机结构所处的工作姿态有关。臂架进行水下破岩作业时,位于水面以下的部分会受到水流的冲击作用,位于水上的结构将受到风力作用。迎风面积取垂直于臂架系统变幅平面,用S1 表示,根据相关标准,风力系数c=1.5,风压q=267.8 N/m2,
故风载荷
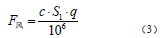
迎水面积同样取垂直于臂架系统变幅平面,迎水面积S2,参考风力系数c=1.5,水压 , 水流速
度v=3.3 m/s,则水流冲击载荷
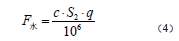
迎风阻力和水流冲击力的合力F=F风+F水。
迎风阻力和水流冲击力对挖泥机臂架系统结构作用的加速度
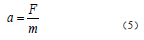
4)船舶横倾载荷
挖泥船在进行作业时,一般都伴随有波浪的影响,考虑船舶横倾角度1°,不考虑船舶纵倾(一般船舶左右摇摆即横倾角度明显大于纵倾角度),重力加速度沿水平方向X 轴的加速度分量

重力加速度沿竖直向下方向Y 轴的加速度分量

3.3 载荷组合
挖泥机破岩作业载荷组合见表1。
4 动力学仿真及分析
根据所述5 种典型工况和表1 的载荷组合, 在ADAMS 软件内对臂架刚柔耦合模型施加边界条件,进行动力学仿真分析[3],本文只展示了工况1 最低和最高破碎锤作业频率的分析结果。
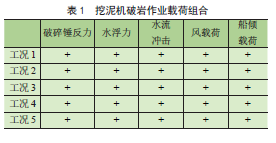
4.1 工况1 破碎锤作业频率250 次/min
工况1 作业频率为250 次/min 时,挖泥机臂架系统整机应力云图见图3。对应力值较大的节点信息进行提取,如图4 所示。
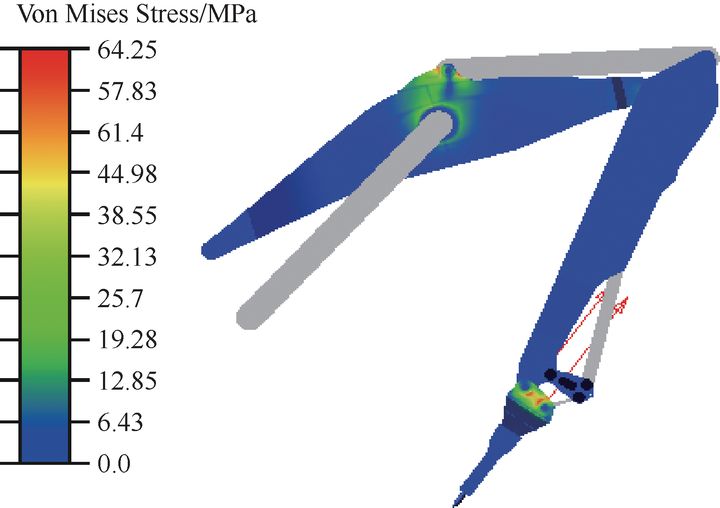
图3 工况1 作业频率250 次/min 整机应力云图

图4 大臂、小臂、支承架最大应力节点动态应力曲线
1)最大应力节点出现在破碎锤支承架上, 最大应力值在0 时刻出现, 说明此工况下破岩作业的初始瞬时阶段有较大的冲击;
2)各个柔性体构件的最大应力值并不是出现在同一时刻;
3)大臂和破碎锤支承架应力值较大,小臂应力值适中,连杆的应力值很小,说明此工况下,大臂、破碎锤支承架以及小臂为主要的承载构件;
4)0 时刻之后,破碎锤支承架上节点应力迅速减小,大臂上节点应力由较大值迅速减小到一较稳定值后呈正弦波动变化, 小臂上节点应力由较小值迅速增大到一较稳定值后呈正弦波动变化,大臂、小臂、支承架明显受到载荷冲击;
5)三条曲线0 时刻载荷的骤变反映出,破碎锤破岩初始阶段臂架系统受到载荷的冲击作用较明显,经过较短时间后节点应力均趋于稳定,呈正弦变化波动,臂架系统整体受载良好。
通过对臂架系统液压缸组的约束铰点进行监测,得到液压缸组(大臂液压缸、小臂液压缸、铲斗液压缸)的受力曲线,如图5。可以发现:1)初始时刻大臂液压缸和小臂液压缸受到载荷波动变化非常明显,载荷波动很大,液压缸组结构明显受到初始载荷的冲击,铲斗液压缸受力相对大、小臂液压缸组很小;2)液压缸组的受力在短时间的冲击之后, 都趋于稳定,呈正弦趋势变化。
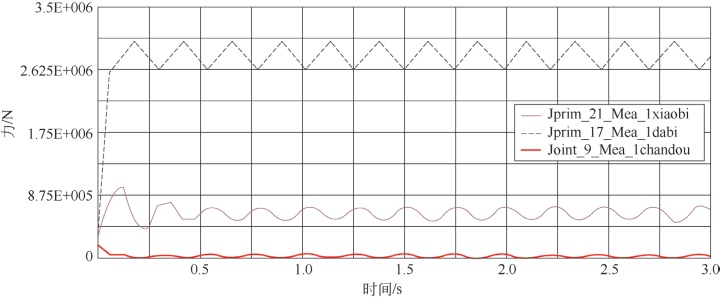
图5 液压缸组受力曲线
4.2 工况1 破碎锤作业频率380 次/min
工况1 作业频率为380 次/min 时,挖泥机臂架系统整机应力云图如图6。对应力值较大的节点信息进行提取,如图7 所示。
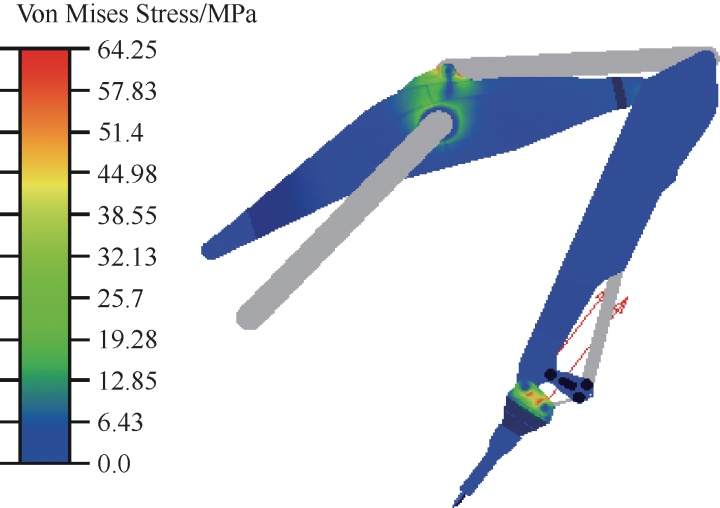
图6 工况1 作业频率380 次/min 整机应力云图
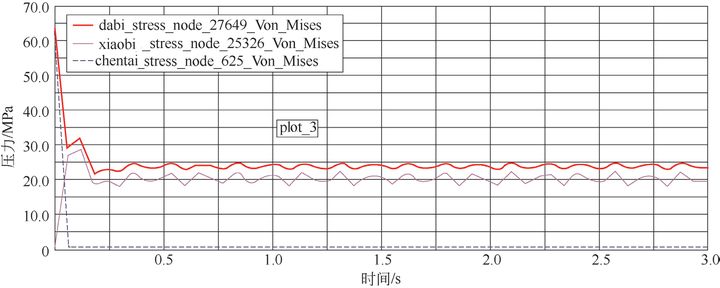
图7 大臂、小臂、支承架最大应力节点动态应力曲线
1)最大应力节点出现在破碎锤支承架上,最大应力值在0 时刻出现;2)各个柔性体构件的最大应力值并不是出现在同一时刻;3)大臂和破碎锤支承架受力较大,小臂受力适中,连杆的应力值很小,说明此工况下,大臂、破碎锤支承架以及小臂为主要的承载构件;4)0 时刻之后,破碎锤支承架上节点应力迅速减小,大臂上节点应力由较大值迅速减小到一较稳定值后呈正弦波动变化, 小臂上节点应力由较小值迅速增大到一较稳定值后呈正弦波动变化,大臂、小臂、支承架明显受到载荷冲击;5)三条曲线0 时刻载荷的骤变反映出,破碎锤破岩初始阶段臂架系统受到载荷的冲击作用较明显,经过较短时间后节点应力均趋于稳定,应力值大小适中,呈正弦变化波动,臂架系统整体受载良好。通过对臂架系统液压缸组的约束铰点进行破岩作业全程力的监测,得到液压缸组的受力曲线,如图8。可以发现:1)初始时刻大臂液压缸和小臂液压缸受到载荷波动变化非常明显, 载荷波动很大, 液压缸组结构明显受到初始载荷的冲击, 铲斗液压缸受力相对较大、小臂液压缸组很小;2)液压缸组的受力经过短时间的冲击之后,都趋于稳定,呈正弦趋势变化。
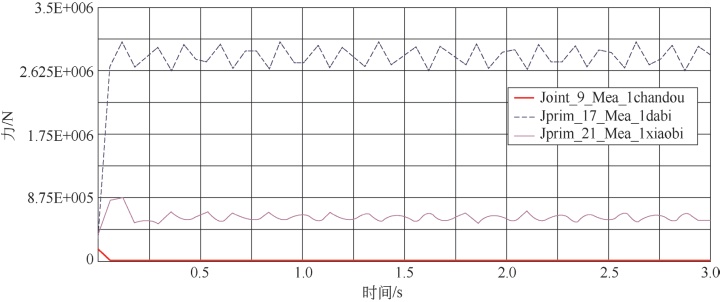
图8 液压缸组受力曲线
4.3 对比分析
1)柔性体结构受力对比对工况1 两种情况下的柔体结构件热点信息进行对比分析:臂架系统在全程仿真时间3 s 内的最大应力值出现在统一构件、同一时刻,均为0 时刻,应力大小均为64.24 MPa,均为同一节点625。但是通过对柔性体构件的热点信息统计(如表2),除了支承架外,大臂、小臂、连杆的最大应力值大小、出现时刻、节点号均不同,说明在作用力相同时,载荷频率的不同对臂架系统的受力有影响。
2)液压缸受力状态对比
通过对比两种频率下液压缸的受力曲线可以得到3组液压缸组的最大推力值(见表3),液压缸组的受力大小基本相同,但是最大推力值存在不同步现象,另外,高频下的液压缸受力曲线的正弦特性有些失真。
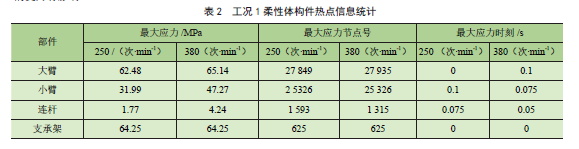
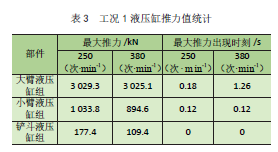
受篇幅限制,本文仅展示工况一的分析情况,其他4 种工况与工况1 的分析结果相似,区别在于最大应力值不同。臂架系统18 m 大臂结构和13.5 m 小臂结构材料均选用D550 材料,破碎锤支承架材料为DH36。根据上述5 种典型工况的动力学计算结果分析,大臂结构和小臂结构及破碎锤支承架动态应力均小于材料许用应力。反铲挖泥机液压缸组的工作压力为29 MPa。各工况下最大油压为17.4 MPa,小于液压缸组的额定工作油压,液压缸组在进行破岩作业时,液压系统承受的压力在许用范围内,液压缸组能满足破岩作业要求。
5 结论
利用有限元分析软件Ansys 建模得到挖泥机臂架系统中大臂、小臂、连杆、支承架的MNF 模态中性文件,进而通过ADAMS 柔性体接口读取文件得到柔性体, 最后完成挖泥机臂架系统的虚拟样机模型, 根据工况要求进行了动力学仿真分析。对动力学分析结果的处理:对柔性体构件提取结构件的最大应力节点表和最大应力节点动态应力曲线。仿真分析结果表明反铲挖泥机臂架系统结构在进行破岩作业过程中大臂、小臂、连杆、支承架等钢结构件的强度满足要求。对大臂、小臂、铲斗3组液压缸组,分别提取了液压缸组的受力曲线,提取各工况下各液压缸的受力最大值换算得到的最大油压值。仿真计算结果表明,三组液压缸组均受载良好。对加装破碎锤后反铲挖泥机臂架系统动力学计算校核结果表明,“津泰”船反铲机加装液压破碎锤在结构上是可行的,能够满足破碎锤水下施工的破岩工作。
参考文献
[1] 戴洪光. 基于ADAMS 平台的柔性体仿真理论的若干研究[D]. 合肥:合肥工业大学,2008.
[2] 李华帅. 基于ADAMS 的滚子夹套式回转支承的动态仿真[J]. 港口装卸,2015(3).
[3] 郭卫东.虚拟样机技术与ADAMS应用实例教程[M].北京:北京航空航天大学出版社,2008.